Case Study:
Emissions from primary bags leading to blocked HEPA filters
Location:
- UNITED KINGDOM
Operation:
Welding & Arc Air Cutting
Dust type:
Manganese dust

Problem:
Emissions and high level of maintenance caused by:
- Bleed through from abrasions in bags caused by metal supports in baghouse
- Fine particulate leaking via stitch holes on conventional bags
- Cell plate has metal burrs, not completing seal with snapband on conventional filter bag
- Regular check for leaks necessary due to HEPA-filters in secondary stage
Solution:
Pleated bags from with spunbond media with ePTFE membrane
TECHNICAL FACTS |
||
BEFORE | AFTER | |
Bag solution | Pleated bag solution | |
Dust type | Manganese fumes | |
Filter type | Filter bag | Pleated Bag |
Media/cloth type | Needle felt with ePTFE membrane | Spunbond Polyester with ePTFE membrane |
Length | 3.000mm | 1.355mm |
Number of bags/cartridges | 408 pcs | 408 pcs |
M² in each bag/cartridge | 1,14m² | 1,96m² |
M² in unit / air volume | 465m² / 25.000m3/h | 800m² / 25.000m3/h |
Advantages:
Decreased emissions on the HEPA-filters and in the working area due to following advantages:
- Shorter filters removed the filtermedia from abrasion zone at the metal support
- No leakage from stitch holes due to different type of media and production process
- Flexible PU-top makes leakage-free mounting possible despite the metal burrs
Longer lifetime of filters due to:
- 42% increased media surface = lower ATC-ratio
- Larger drop out box increases "gravity filtration", a larger amount of the heavier dust particles falls into the hopper even before reaching the filter media
No in-between maintenance/inspections necessary!
Before:



Solution after:

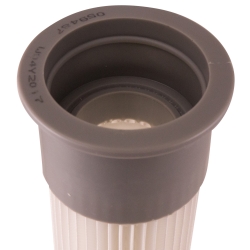

Sales Representative:
RS