Case Study:
Low suction in plasma cutting baghouse
Location:
- DENMARK
Operation:
Suction from plasma cutting machines
Dust type:
Stainless steel, black steel and alu - cut in thick plates

Problem:
Customer had issues with pleated bags from competitor:
- Unacceptable low suction at cutting machines, especially after starting with night shift in Production hall.
- Thick raw plates created high dustload when cutted
- Filters changed once pr year
- 4 years ago a spark causing a fire in the baghouse resulted in change to pulsing with Nitrogen, but type of filter media was not changed
Solution:
- Specialists from Nordic Air Filtration assisted the reseller at inspection on endusers site
- Pleated bags with increased filter surface and ePTFE-membrane on polyester base media (spark resistant, to minimize risk of fire) was installed August 2017
- Guidance on the use of PreKote was given
- September 2018, one year after installation, customer was so satisfied with the solution that they bought same filters for their other similar baghouse on site
TECHNICAL FACTS |
||
BEFORE | AFTER | |
Airflow in unit | 25.000 m³/hour | |
Dusttype | Plasma cutting in Stainless Steel, black and alu | |
Collector running hours/year | 8.736 | |
Filter model | Pleated bag from competitor | CPB154 |
Media/cloth type | Polyester w. PTFE Coating | Polyester w. PTFE Membrane (NA-900) |
Length | 2.000 | 2.070 |
Number of bags/cartridges | 216 | 216 |
M² in each bag/cartridge | 3,07 | 5 |
M² in unit | 663 | 1080 |
Air-to-cloth ratio (m3/m2/h) | 37,70 | 23,15 |
Bag house type | Pulsejet | Pulsejet |
Advantages:
- Lower dP for a longer time
- Optimized suction in Production hall
Before:

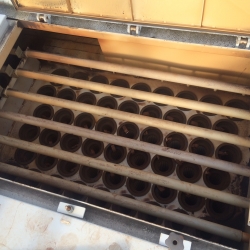

Solution after:

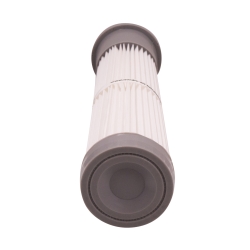

Sales Representative:
KMF