Case Study:
Milling of TiO2 - New dustcollector
Location:
- SLOVENIA
Operation:
TiO2 Milling
Dust type:
TiO2
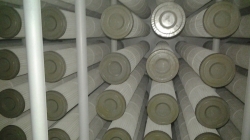
Problem:
Former solution in reverse air dust collector with ring bags gave following problems:
- Lifetime only 1 year
- Emission above 20mg/m3. Below 10mg/m3 was required.
Solution:
New dust collector from OEM with Pleated Bag from Nordic Air Filtration installed March 2016.
TECHNICAL FACTS |
||
BEFORE | AFTER | |
Bag filter | Pleated bag solution | |
Airflow in unit | 24.000 m³/hour | |
Dusttype | TiO2 mill | |
Collector running hours/year | 24/7 | |
Filter model | Reverse air dust collector with ring bags | New pulse jet dust collector with Pleated Bags |
Media/cloth type | Polyester | Polyester with Weltech bands |
Length | 3.300 | 2.000 |
Number of bags/cartridges | 600 | 600 |
M² in each bag/cartridge | 1,8 | 3,67 |
M² in unit | 359 | 540 |
Air-to-cloth ratio (m3/m2/h) | 66,85 | 44,44 |
Dimension of dust collector (meter) | 2,5 x 9,5 x 5 | 2,4 x 4,8 x 5 |
Advantages:
- New dust collector occupies half the space compated to old dust collector
- Lower emission due to spun bond media. Emission in June 2017: 3,8mg/m3 - almost three times as low as required
Solution after:
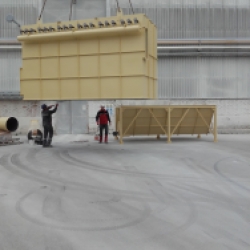
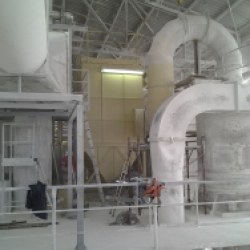
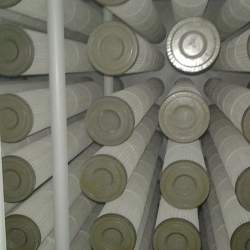
Sales Representative:
MG