Case Study:
Pulse cleaning problems & short life cycle of filter bags solved with spunbond polyester pleated bags
Location:
- GERMANY
Operation:
Foundry & Grinding
Dust type:
Cast iron grinding powder
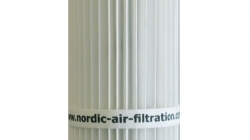
Problem:
- The use of 160x5000mm polyester felt filter bags caused problems as dust particles would not release from the felt media
- The result was pulse cleaning difficulties and rapidly increasing deltaP leading to a too short life cycle of the filter bags
Solution:
- Spunbund polyester, which is a surface filtration media, is more efficient for pulse cleaning keeping deltaP low for substantially longer than the felt media.
- Simultaniously, as a consequence of upgrading to pleated bag filters, the filter surface area has increased by 55% equal to an air to cloth ratio of 50 m3/m2/hour (2.7:1).
- More efficient pulse cleaning has resulted in decreased energy costs as well as longer filter life cycle.
TECHNICAL FACTS |
||
BEFORE | AFTER | |
Bag solution | Pleated bag solution | |
Dusttype | Cast iron grinding powder | |
Filter model | Filter bag | Multifit Pleated Bag |
Media/cloth type | Needle felt | Polyester |
Length/mm | 5000mm | 2000mm |
Number of bags/cartridges | 300 | 300 |
M² in each bag/cartridge | 2,5m² | 4,5m² |
M² in unit | 750m² | 1350m² |
Advantages:
- Longer life cycle of filter
- Better air flow and reduced DeltaP due to more efficient pulse cleaning
- Energy savings on main fan & pulse cleaning