Case Study:
Pleated bags installed in shaft furnace at steel plant
Location:
- CHINA
Operation:
Shaft furnace for pellet firing
Dust type:
Ferric oxide, manganese oxide

Problem:
- The overall steel group is focusing on lowering emission
- Emission was about 20mg/m3, which is above the emission standard.
- Goal: emission lower than 5mg/m3
Solution:
Replacing 1.152 bags with 1.152 pleated bags.
Installed October 2018.
TECHNICAL FACTS |
||
BEFORE | AFTER | |
Bag filter | Pleated bag solution | |
Airflow in unit | 280.000 m³/hour | |
Dusttype | Ferric oxide, manganese oxide. Shaft furnace for pellet firing | |
Collector running hours/year | 8.000 | |
Filter model | Filter bag | CPB |
Media/cloth type | Polyester+PTFE | Polyester w. PTFE membrane |
Length | 6.000 | 2.000 |
Number of bags/cartridges | 1.152 | 1.152 |
M² in each bag/cartridge | 3,00 | 5,60 |
M² in unit | 3.456 | 6.400 |
Advantages:
By replacing the existing filter bags with Pleated Bags from Nordic Air Filtration the following results were obtained:
- Decreasing of filter length, 2m vs 6m = 4m higher drop-out box underneath the filters
- The PU-top fit easily to the tube sheet
- Spunbund polyester, which is a surface filtration media, is more efficient for pulse cleaning keeping deltaP low for substantially longer than the felt media
- As a consequence of upgrading to pleated bag filters, the filter surface area has increased by 50%
- Weldtech technology (ultrasonic welded bands) ensures perfect fit of the bands and equal pleatdistance
- Lower emission than with conventional filter bags. Emission after: 3,9mg/m3
- Lower air-to-cloth ratio and lower dP, 700pa (after) vs 1800pa (before), provide significant cost saving of fan
Solution after:

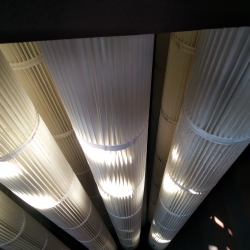
Sales Representative:
BB